What is Industrial Hygiene?
Industrial hygiene is the science and art of anticipating, recognising, evaluating, and controlling hazards in the workplace. Industrial hygiene provides technical assistance and expertise for controlling workplace hazards.
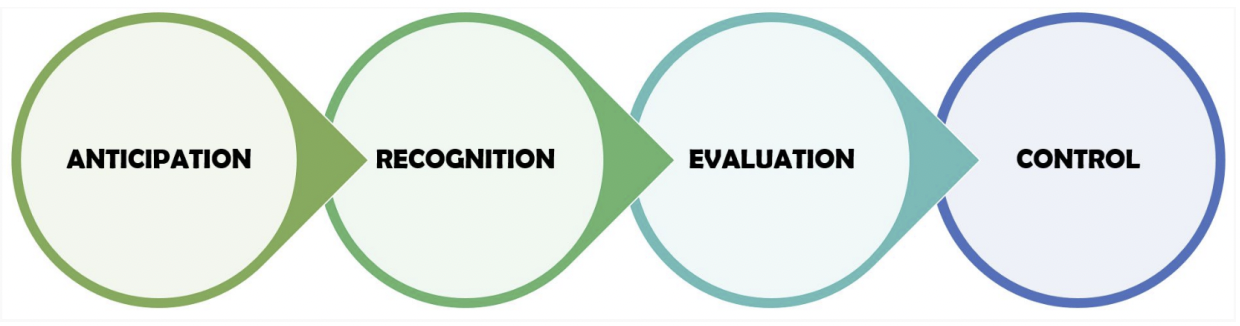
Anticipate: The process of sensing the presence of potential hazards without actually observing them in-person.
Recognize: The process of identifying a hazard when it's observed at workplace.
Evaluate: The process of determining the harm that hazard can cause and how severe the harm could be.
Control: The process of putting measures into place to eliminate or to minimize the potential of the hazard to create harm, such as injury or illness.
What are the Responsibilities of an Industrial Hygienist?
IH helps in advising the management to resolve occupational health issues.
Identifies and evaluates chemical and biological dangers such as air quality, ergonomic challenges, or dangerous sound levels.
Investigating and examining the workplace for hazards and potential dangers.
Implements applicable occupational health and safety regulations and procedures.
Conducting regular audits in the work premises.
executing studies in order to monitor and evaluate workers exposure to health risks.
Assessing and interpreting research data, and reports.
Making recommendations on improving the health and safety of workers.
Recommends precautions and corrective actions that should be taken in response to identified hazards.
What are the work concerned with the field of Industrial hygiene?
Occupational Diseases (Silicosis, Coal miner’s Disease, Asthma, etc)
Air quality assessment
Hazardous substance & waste management
Controlling Physiological disorders ( Work-related stress)
Radiation management
Biological hazards (virus, bacteria, etc) and Chemical hazards (over exposure of harmful chemicals)
Noise control
Control of Heat Stress
Control of Ergonomics and Work load hazards
What are Hazards and its types in a workplace?
A hazard is any object, situation, or behavior that has the potential to cause injury, ill health, or damage to property or the environment. Hazards can appear in many occupational circumstances.
Some hazards are acute and pose danger to the health and physical integrity of the worker in the work place. Others take a longer time to materialize and may have a cumulative effect, as is the case for certain chemicals, vapors, dusts, and radiation that may lead to chronic medical conditions following repeat or prolonged exposure.
Types of Hazard:
Chemical Hazards:
Harmful chemical compounds in the form of solids, liquids, gases, mists, dusts, fumes, and vapours exert toxic effects by inhalation (breathing), absorption (through direct contact with the skin), or ingestion (eating or drinking). Exposure to chemicals can cause acute or long-term detrimental health effects. For information of chemical hazard Material Safety Data Sheet (MSDS) is available.
Biological Hazards:
Biological hazard include bacteria, viruses, fungi, and other living organisms that can cause acute and chronic infections by entering the human body through inhalation, injection, ingestion or absorption.
Physical Hazards:
These include excessive levels of ionizing and non-ionizing electromagnetic radiation, noise, vibration, illumination, and temperature. This type of hazard are very common and its is challenging to avoid them.
Ergonomic Hazards:
Ergonomic hazards are physical conditions that may pose risk of injury to the musculoskeletal system. It include awkward postures, static postures, lifting, holding, pushing, walking and reaching large forces, repetitive motion, or short intervals between activity.
How to control hazards in a workplace?
In order to control hazard in workplace there is a Hierarchy of control given which is a very effective procedure used by the industrial hygienist to minimise and eliminate the hazard in work place. The hierarchy consist of 5 steps.

The hazard controls in the hierarchy are, in order of decreasing effectiveness:
Elimination- It is a very effective method of removal of the hazard from the work place.
Substitution- The process of replacing the hazard with something that would cause less harm. Replacing benzene with toluene would cause less harm to the workers.
Engineering controls- The process of using engineering to eliminate hazard by isolating or providing ventilation or illumination etc. which would be a effective control
Administrative controls- Controls which alter the way work is performed by introducing policies, training, standard operating procedures/guidelines, personal hygiene practices, work scheduling process in workplace.
Personal protective equipment- PPE’s provides safety at individual level. It includes helmets, respirators, ear cuffs, body suits, etc. PPE’s should be used as last line of defence as it is the least effective of all controls.